Introduction
Today, in New Zealand, housing is being
built according to a set of rules with the
stated aim of protecting consumers.
Nothing could be further from the truth.
The Building Act is no more than window
dressing for a set of rules that vastly
increases the cost of building while
reducing the lifespan of a building to
little more than a throw away consumable.
The Building Act sets out the overall aims
and objectives, enforceable by law.
The regulations formed under that Act are
supposed to give some guidance as to how
those worthy aims might be met.
To the contrary, the regulations illegally
create "safe havens" for appallingly bad
building products and practices and
indemnify the purveyors of said products
from being sued when it all hits the fan.
Examples:
Two notable examples are leaky flashings and
inadequate bracing. Together these shorten
the life of a building by eating away at the
structure and creating damage in an
earthquake that is so costly to repair that
it is cheaper to demolish a house than
repair it, at enormous expense to the
economy.
Big players in this massive scam on the New
Zealand homeowner and taxpayer are the likes
of Hardies and Winstones, two organisations
without moral compass who, combined with a
legislature that is too busy saving face to
care about taking any serious action to
avert disaster, are hell bent on reducing NZ
building stocks to more of a liablility than
an asset.
Flashings:
Here is a leaky flashing, courtesy BRANZ I
believe (off the Internet), typically used
for "Linea Weatherboard," another shonky
Hardie's product.
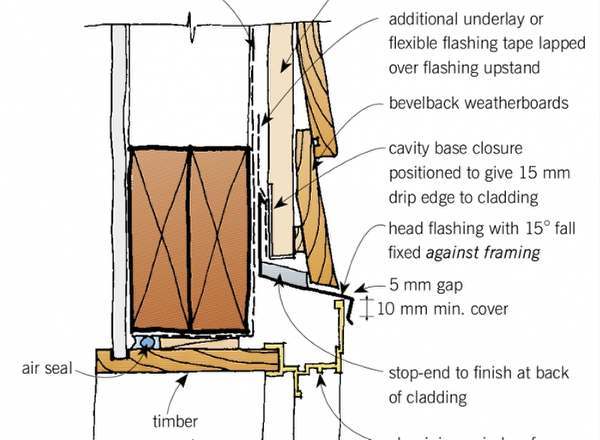
This
detail is the very same detail identified in
the leaky homes scandal as allowing moisture
to sit against timber framing and causing
dry rot.
In a stroke of genius, not, the Branz detail
even emphasizes that the flashing
should be "against framing."
Instead of changing the detail to something
that would work, the regulators in a act of
gross stupidity have enshrined this awful
detail into law as an "acceptable solution,"
meaning that local councils who issue
building consents will virtually insist that
this detail, and this detail alone, will or
must be used, even though it leaks, rather
that an "alternative" flashing that won't
leak.
How does it leak? Weatherboards discharge
water to the outside of a building. If you
cut a slot or rebate into those boards, they
will leak. If you fix flashings to framing,
the framing will rot.
I, along with others, have first hand
knowledge of the damage caused by these
flashings. What first looks to be blistering
paint on the outside of a house turns out to
be far more extensive once the weatherboards
are removed, with rot in lintels, doubled
studs, wall framing, bottom plates, and on
it goes.
Adding a cavity to let the water "drain out"
has to be the dumbest idea yet.
The traditional system, with a proven track
record of not leaking, works with the
weatherboards, not against them, by
discharging moisture to the outside rather
allowing it back against the framing.
There is no way any consent authority today
is going to allow a traditional flashing.
There are no polytechs teaching this correct
method. The builders who know how to make a
decent flashing are all either retired or
have found, like me, that the uphill battle
against idiots with excess power and
stopwork notices is impossible to win.
Bracing:
In similar fashion to Hardies and their
"approved" leaky flashings, Winstone
Wallboards would like consumers to believe
that using their products to brace a
building will make it "safe."
This lie fails to distinguish between
bracing and stiffening.
A braced structure is plastic, that is it
will deform under load and return to its
original shape when the load is removed.
All buildings move to a smaller or greater
extent. They move under wind load,
earthquake load, heat and cold, and move
with the seasons as the ground around the
building swells and contracts with moisture.
They are supposed to flex.
Traditional bracing holds parts of the
building upright. Between braces the
building can move whichever way it wants.
Prior to gib linings we had scrim and so on.
With the introduction of paperfaced plaster
board, builders only nailed sheet edges and
intermediates, i.e. only nailed into studs.
There was no nailing to either top or bottom
plates.
Instead of nailing to the top plate, the
scotia was nailed to studs which had the
effect of restraining the top edge of gib
sheets but still allowed some expansion of
the sheet. Similarly the perimeter of the
ceiling gib was not nailed, the sheet edges
simply resting on the scotia and able to
expand and contract.
The bottom edge of gib sheets were not
nailed. The skirtings were nailed to studs
and this had the effect of constraining the
lower edge of gib sheets while still
allowing room for the gib to move.
Simple put, wall linings were hung.
In this way bracing kept a building upright
and the linings were fixed in a way that
allowed for plastic movement. It worked very
well.
Today you could not get a consent to do that
because these perfectly adequate timber
braces are so downgraded by the "rules" as
to make it impossible to meet consent
requirements.
That downgrading process plays to the
advantage of Winstones.
The lie by Winstones is that their products
are bracing. They are not.
Sheet products are stiffening and have no
ability to behave in a plastic fashion. They
are a "use once" product that, having gone
through a major earthquake, cannot take the
same loads twice. They are throw away
products, like the houses they are installed
into.
Note:
This page will stay on the web. The Minister
for Building and Construction, the Hon Chris
Penk, has been advised.
Hardies is James Hardie Industries PLC who
operate out of Ireland (and avoid tax in the
Netherlands) and have walked away from much
of their responsibility for asbestos related
deaths caused by a failure to advise
consumers of the health risks associated
with their asbestos sheet products, and also
seem to have walked away from their leaky
flashings around Harditex sheet products, a
NZ Judge incorrectly finding the problems
were related to bad building methods rather
than Hardies product failures (how wrong can
a person be?). Winstones is owned by
Fletchers who just love to hold the building
industry to ransom during supply shortages.
Thugs, both of them.
Remedy:
At the very least there must be a change to
the regulations to make traditional head
flashings part of the acceptable solutions
and traditional let-in timber bracing
(assuming stud sizing of at least 100mm
depth to receive them) must be credited with
the ability to do the job.
Posted
4th Feb 2024
The bad grammar and typos are all mine. Despite
that, I hope the message is clear.
The author is formally qualified with a
bachelor's degree in architecture (1980) and a
diploma in building surveying (2012).
email:
sphlat@actrix.co.nz
.